FMax 6000 - Sir Meccanica
FMax 6000
Beschreibung Und Anwendungen.
New generation machine tools, entirely managed by an electronic control panel, which allow the most varied and sophisticated machining operations on the surfaces of large cylindrical tubular bodies, obtaining extremely high levels of finishing and precision.
The FMax 6000 model can be used for the following processes:
- GENERAL FACING;
- MILLING;
- GROOVING;
- CHAMFERING;
- DIE-SINKING MACHINING;
- BEVELING.
Facing Diameters:
Ø 1900mm - Ø 6000mm (74.80" - 236.22")
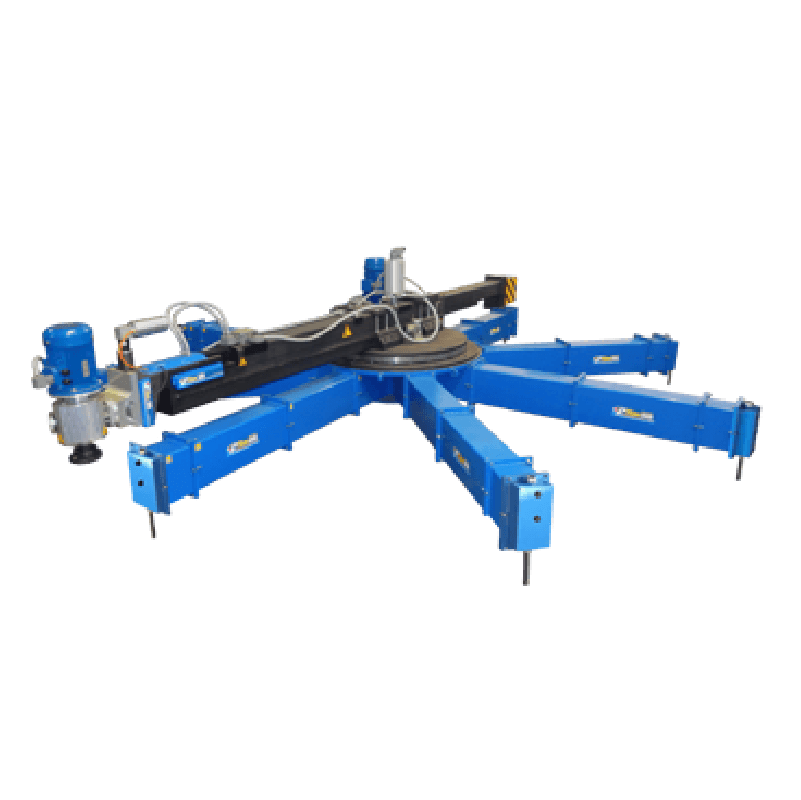
Produktdetails
The main features of our FMax series are:
Anchoring and centering system with 4-spoke MODULAR star. Installation in any position, even vertical and/or tilted thanks to the system with slotted anchoring brackets. The 4 spokes of the star allow for easy and fast centering and adjustment as they are positioned at 90° opposite ends. The machine is anchored to the punch terminals on each spoke (present with both radial and axial effect).
Central body SLEWING BEARING BASE with double slewing ring system with opposing effect to eliminate clearance.
Rotation motion transmission system with reduced clearance. An adjustment system allows for clearance adjustment even in the presence of wear due to time and use. In this way, angular clearance is reduced to a minimum.
The rotation reducer, as well as the spindle, work in an oil bath in a watertight case. All axes are moved on ground guides and recirculating ball screws with long-lasting lubrication.
The milling cutter arm as well as the counterweight arm are radially adjustable according to your needs (pre-positioning). The adjustment, once the fastening systems have been loosened, is carried out via a manual rack system. The position of the counterweight must be determined based on the position of the cutter arm so that the machine, especially if it is not positioned horizontally, is always balanced.
The motors are controlled electronically by the control unit and by means of a rotating electric joint positioned at the center of the machine body. This allows the machine to perform infinite revolutions around its axis without winding the electric cables.
The X-axis stroke (radial) allows, in a single work step, to pass from the minimum diameter to the maximum possible diameter, covering the entire working range. Both axes, the rotation of the machine (X) and the rotation of the milling cutter (Z - spindle) are electronically controlled by the control panel in speed (from 0 to max) and in rotation direction (right or left) with centesimal precision. The Z-axis can also be moved manually directly from the Z-axis handwheel. Each turn of the handwheel corresponds to a movement of approximately 0.1 mm.
The spindle has an attachment for the BT40 cutter.
The FMax series has been designed and created to perform on-site operations in order to avoid economic or logistical challenges related to moving equipment, their components, or structural parts from their original location. With perfectly balanced inertia, it can work in any position: horizontal, vertical and oblique.
Its innovative construction structure allows the machine to safely absorb radial and axial stresses and overturning moments, reducing harmful vibrations to a minimum.
The FMax 6000 machine tools can also be used as precision drilling/tapping machines. Once the diameter and number of holes to be drilled in a circular series have been established, the control panel automatically calculates all the drilling positions: just like a real electronic indexing head.
The machine tools of the FMax series can be customized, according to the details and geometric specifications provided by the customers, which allow the technical staff to design a solution suitable to their needs.
The control panel adapts in height and inclination to the operator's needs, providing maximum comfort in handling and use.
There are four control zones, one for each machine movement:
• [S] - cutter rotation;
• [R] - machine rotation;
• [X] - radial feed;
• [Z] - axial feed.
It is possible to independently set the direction through the manual left-off-right selector and the speed through the multi-turn potentiometer (for each movement). The translations of the radial feed [X] and axial feed [Z] axes can be managed via the rapid button.
For each of the movements there is an ST.P. bar. and a status display for diagnostics of the operating status. Each control zone is equipped with its own display which indicates the feed speed and rotation revolutions per minute.
On the control unit there is also a display for the electronic positioner, which allows you to monitor the distance traveled by the tool and to view and set the travel limits of the X and Z axes. A further button allows to view on the display the speed in mm/min of the X and Z axes and in rpm for the spindle (S) and the rotation of the machine (R).
The mains voltage of the machine is 400 V 3ph˜ 50/60 Hz.
Fotogalerie
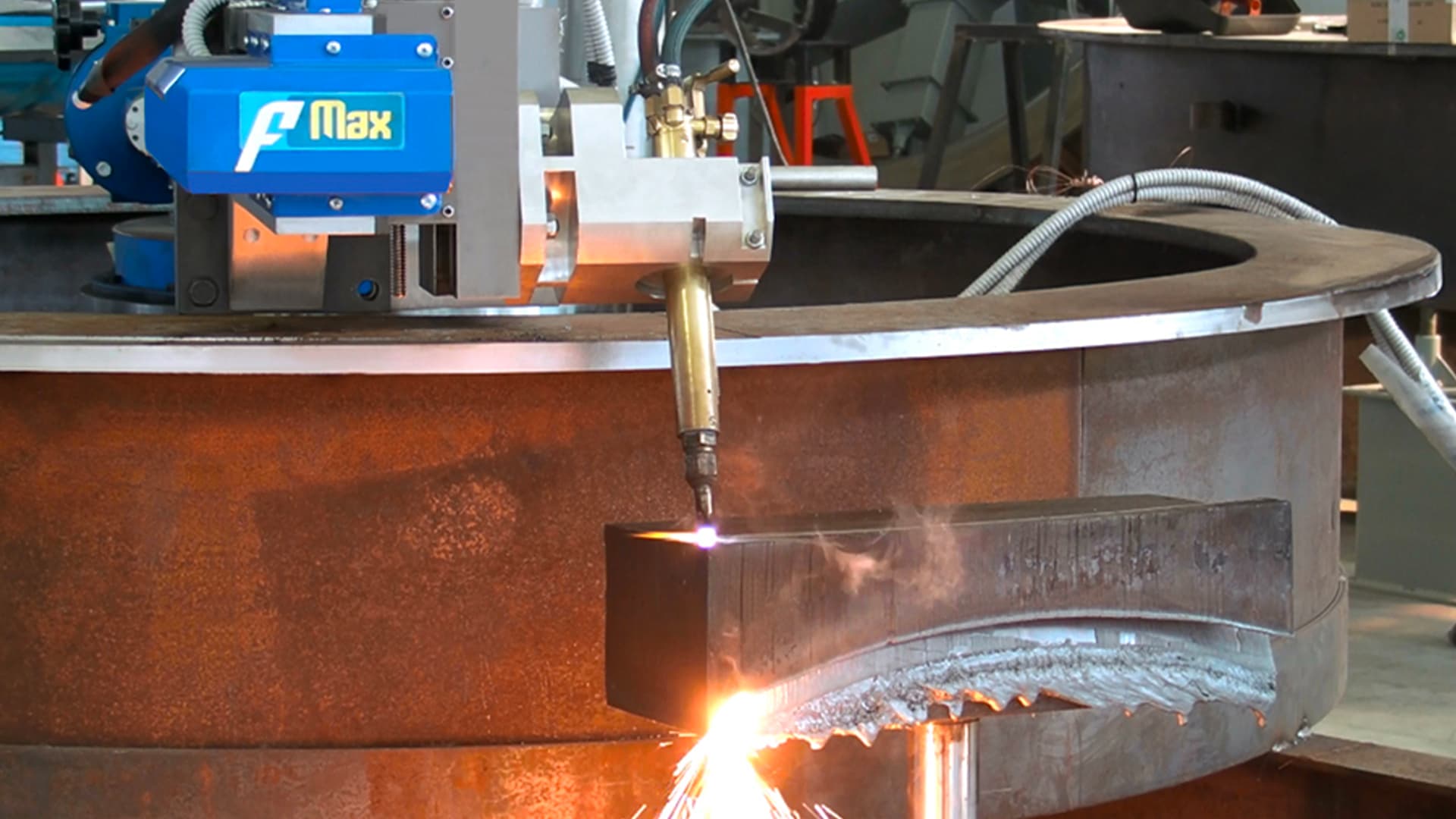
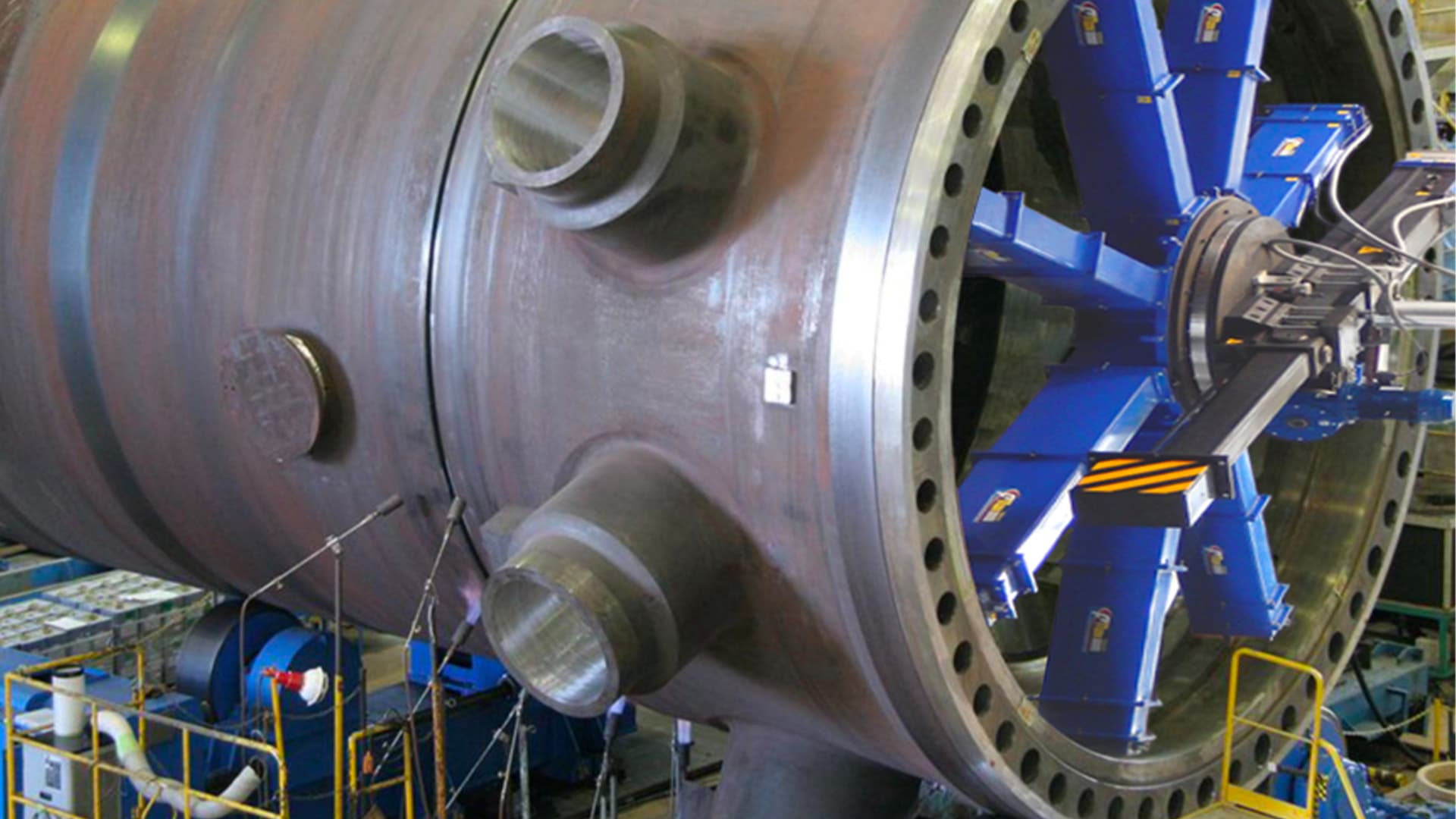
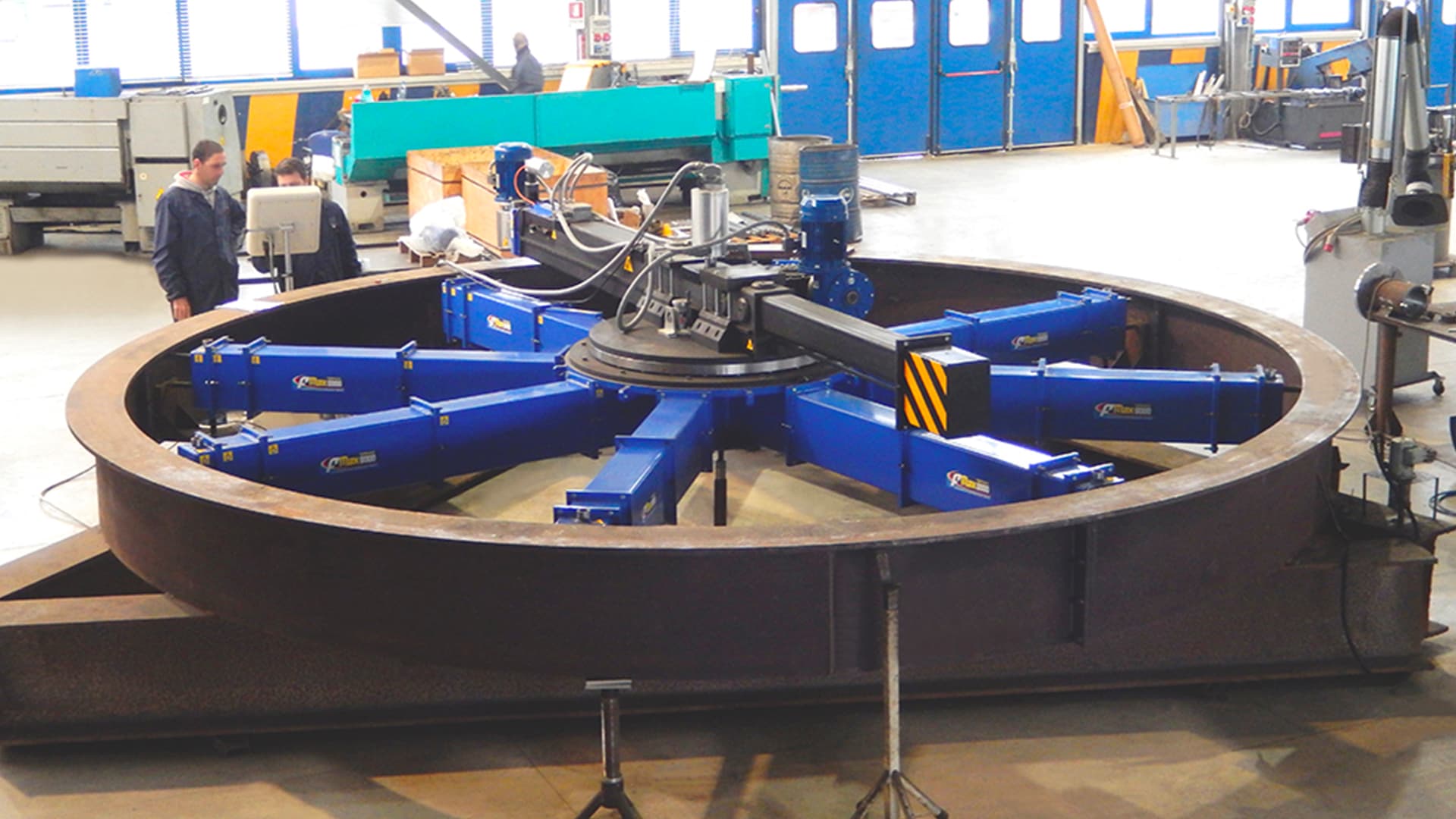